Hydraulic systems have a range of applications, from lifting heavy loads in construction to deploying landing gear in aircrafts. At the heart of these complex yet effective systems are
hydraulic valves – controlling the flow, pressure and direction of hydraulic fluid and enabling
smooth and precise operations. But how exactly do hydraulic valves work?
At Lesjöfors, we’ve been manufacturing precision-engineered springs and pressings for the
hydraulics industry for decades. In this blog, we’ll explore the basics of hydraulic valves, their
types and their functions.
The Basic Working Principle of a Hydraulic Valve
The purpose of a hydraulic valve is to regulate the flow and pressure of fluid within a hydraulic system, allowing for precision control.
How Does a Hydraulic Valve Work?
A hydraulic valve controls fluid flow using a movable part like a spool or poppet. When activated, this part shifts to open or close passages, directing the fluid to different parts of the system. This adjustment controls both the flow rate and pressure, ensuring smooth and safe operations, even as system conditions change.
Types of Hydraulic Valves and Their Functions
Directional Control Valves (DCVs)
Directional Control Valves (DCVs) in hydraulic systems direct the flow of fluid to different parts of the system and control the movement of actuators, such as cylinders and motors. DCVs can have multiple positions and configurations, allowing operators to start, stop, or reverse fluid flow as needed.
Check Valves
Check valves are one-way valves that allow hydraulic fluid to flow in a single direction while preventing backflow. They help maintain pressure stability and protect system components from potential damage caused by reverse flow.
Two-Way Valves
Two-way valves have two ports — one for fluid entry and one for exit. They function as simple on/off switches, allowing or blocking flow within a hydraulic system.
Three-Way Valves
Three-way valves have three ports, enabling them to direct hydraulic fluid between two different pathways. They’re commonly used to alternate pressure between two actuators.
Four-Way Valves
Four-way valves have four ports: two for the actuator and two for fluid supply and return. They mainly control double-acting cylinders and hydraulic motors, allowing movement in both directions.
Solenoid Valves
Solenoid valves use an electrically operated coil to control fluid flow. When energized, the coil moves a plunger or spool inside the valve, opening or closing specific flow paths.
Spool Valves
Spool valves control fluid flow by shifting a cylindrical or sliding spool inside the valve body. The spool’s position determines which ports are open or closed, regulating the direction, pressure, and volume of fluid in the system.
Pressure Control Valves
Pressure control valves regulate pressure levels to ensure safe and efficient operation. They open, close or modulate flow based on pressure conditions, protecting components from damage and optimizing performance.
Relief Valves
Relief valves protect hydraulic systems from excessive pressure by opening when limits are exceeded, allowing excess fluid to return to the reservoir.
Pressure Reducing Valves
Pressure reducing valves maintain a lower, controlled pressure in a specific part of the hydraulic circuit by restricting flow when necessary.
Sequence Valves
Sequence valves ensure hydraulic operations happen in a specific order by allowing fluid flow to a secondary actuator only after a set pressure is reached.
Counterbalance Valves
Counterbalance valves prevent uncontrolled movement in a hydraulic system by maintaining back pressure in a circuit, typically controlling the descent of heavy loads.
Unloading Valves
Unloading valves divert excess fluid to the reservoir at low pressure when the system demand is reduced, preventing energy waste.
Proportional & Servo Valves
Proportional and servo valves are advanced control valves used in hydraulic systems.
Proportional Valves
Proportional valves control the flow or pressure by varying the valve position according to the electrical input signal. This enables smooth and adjustable operation of actuators and better control over speed and force in applications like industrial automation.
Servo Valves
Servo valves have more precise control, responding to small electrical signals and making fi ne adjustments to fluid flow. High-performance systems in aerospace and robotics often use these valves as they require high accuracy and quick response.
Flow Control Valves
Flow control valves in hydraulic systems modulate the fluid flow rate, controlling the speed and movement of actuators so they operate smoothly and efficiently.
Throttle Valves
Throttle valves control fluid flow by restricting the passage size, enabling precise adjustments to actuator speed and performance.
Needle Valves
Needle valves use a tapered needle to fi ne-tune the fluid flow, allowing for ultimate control over low flow rates in the system.
Pressure Compensated Flow Control Valves
Pressure-compensated flow control valves automatically adjust the valve opening to maintain a constant flow rate despite pressure fluctuations, ensuring steady performance.
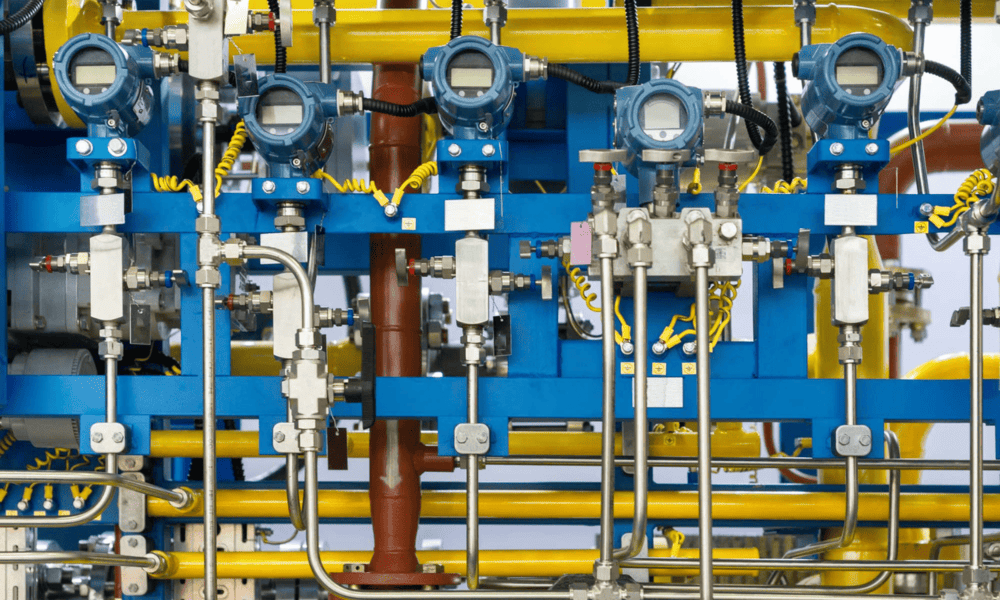
Core Components of a Hydraulic Valve System
Actuators
Actuators convert hydraulic energy into mechanical motion, driving the movement of components.
Hydraulic Pump
The hydraulic pump generates the necessary flow and pressure by converting mechanical energy into hydraulic energy.
Hydraulic Fluid
Hydraulic fluid transfers power throughout the system, lubricates components and helps dissipate heat.
Reservoir (Tank)
The reservoir stores excess hydraulic fluid, maintains fluid temperature, and provides a buffer for system pressure variations.
Spools, Seals & O-Rings
Spools, seals, and O-rings work together to control fluid flow paths and prevent leaks, ensuring smooth and efficient operation.
Springs
Springs help return valve components to a closed position, contributing to precise control and reliable system performance.
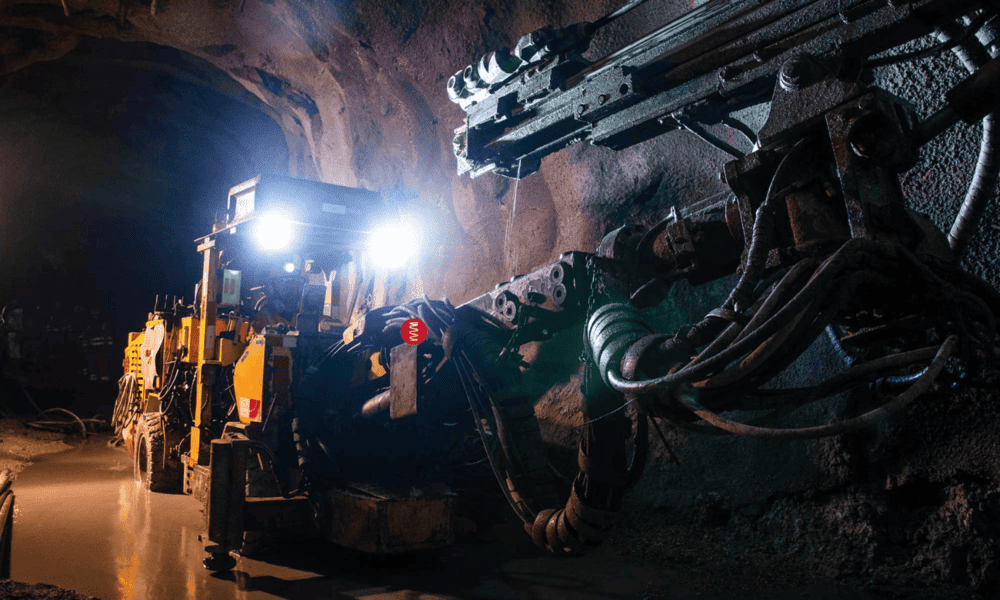
Applications of Springs in Hydraulic Systems
Valve Actuation Systems
Springs are a key component in valve actuation systems and they play an essential role in controlling mechanical operations and the flow of fluids via valves and actuators.
Suspension Systems
Springs in hydraulic suspension systems absorb shock and dampen vibrations from uneven surfaces. They help maintain vehicle stability and balance by cushioning impacts, reducing stress on hydraulic components, and ensuring smoother, safer movement.
Construction Machinery
In construction machinery, springs are used within hydraulic systems to absorb shocks and reduce vibrations during heavy operations. They stabilize components by counterbalancing forces and helping the quick return of moving parts. Springs are an important part of minimizing wear while enhancing reliability and performance.
Agricultural Implements
In agricultural implements, springs support hydraulic systems by absorbing shocks from uneven terrain and reducing operational vibrations. They stabilize actuators, maintain precise control, and ensure consistent performance by balancing forces and facilitating smoother transitions.
Custom Springs for Hydraulic Valve Applications
Overall, a wide variety of valves are used across hydraulic systems, each performing a slightly different function. At their core, all hydraulic valves regulate fluid flow and are essential to the proper functioning of a system, with springs playing a crucial role in ensuring precise, efficient, and safe operation.
At Lesjӧfors, we have over 170 years of expertise in producing high-quality springs, many of which feature in hydraulic systems across the globe. Our expert engineers are here to develop a custom spring solution tailored to your hydraulic needs — from design and prototyping to testing and manufacturing. Contact us today to discuss.
FAQS
Yes, hydraulic valves may need adjusting to optimize system performance, compensate for wear, or adapt to changing operating conditions.
A hydraulic shut-off valve controls fluid flow by opening or closing a sealing mechanism, stopping or allowing movement within the system for safety, maintenance, or operational control.
A hydraulic check valve allows fluid to flow in one direction while preventing backflow by using a spring-loaded or gravity-assisted mechanism that closes when reverse flow occurs.
You can determine if a hydraulic valve is open or closed by checking the actuator position, monitoring flow and pressure changes in the system, or inspecting indicator markings on the valve body.