Medical device engineering demands uncompromising precision, reliability, and cleanliness, especially when it comes to small yet critical components like springs. From compression springs in inhalers to constant force springs in glucose monitors, these components play a vital role across a wide range of medical devices.
At Lesjöfors, we combine advanced capabilities in cleanroom manufacturing, contamination control, and medical-grade materials to produce springs that meet the strictest medical industry standards. Our custom-engineered solutions are trusted by leading medical device manufacturers across the globe, for applications ranging from autoinjectors to wearable health monitors.
In this post, we’ll explore how springs are used in medical devices, highlight the most common spring types, and examine the materials that deliver the best performance in healthcare environments.
How are Springs Used in Medical Devices?
Springs are used in medical devices to store and release mechanical energy for functions like actuation, dose control, sensor positioning, and needle retraction. Their precision and reliability are essential for ensuring safety, accuracy, and comfort in both wearable and handheld medical equipment.
Key Spring Types in Medical Devices
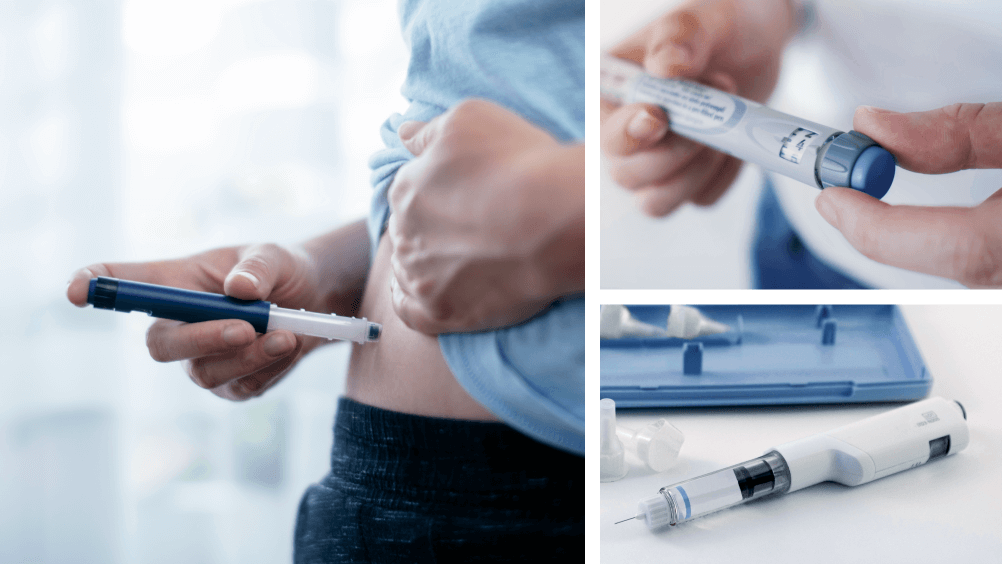
Compression Springs: Dose Control and Actuation
Compression springs for medical devices are fundamental to the safe and accurate function of inhalers, autoinjectors, and wearable systems. These springs compress under load and return to their original shape, delivering the energy required to initiate actions like delivering a dose or retracting a needle.
Power Springs: Sustained Force in Equipment
Power springs for medical devices are designed to deliver sustained mechanical force over a longer duration. They’re commonly found in ‘PowerPacks’ and portable medical equipment, where constant, even torque is critical. These spiral-wound springs allow for energy storage and smooth release, often in confined spaces.
Constant Force Springs: Controlled Torque in Sensors
Constant force springs are engineered to provide precise rotational torque, perfect for medical devices like glucose monitors, wearable sensors, and advanced diagnostic devices. Their ability to maintain repeatable, low-force torsion over many cycles makes them ideal for delicate sensor positioning and patient comfort.
Medical Device Applications
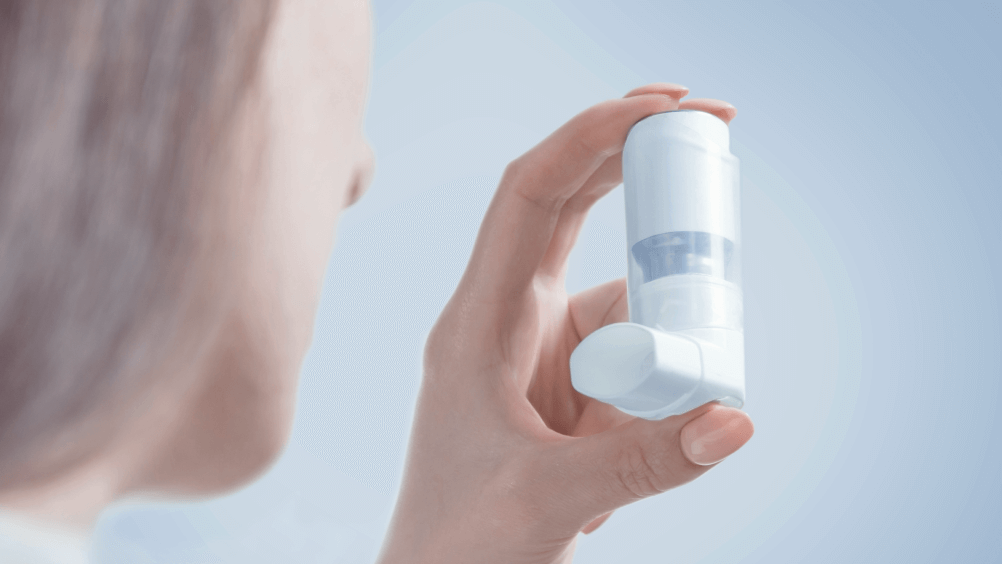
Inhalers: Accurate Dosing and Hygiene
In inhalers, compression springs play a critical role in dose metering and delivery mechanisms. These sterile medical springs must function flawlessly to ensure the patient receives the correct medication amount. Our precision medical springs at Lesjöfors support both disposable and reusable inhaler designs, prioritizing hygiene and user safety.
Autoinjectors: Safe and Reliable Drug Delivery
Springs for autoinjectors must perform without fail, and are often used in emergency or self-administered contexts. Compression and power springs are engineered to activate at the right force and timing to deliver medication safely and completely. At Lesjöfors, we design medical springs with tight tolerances for these life-critical applications.
Glucose Monitors: Sensor Function and Comfort
For wearable and implantable glucose monitors, constant force springs and compression springs ensure consistent sensor positioning and gentle skin contact. These custom medical springs are engineered for durability, comfort, and corrosion resistance, supporting the continuous performance needed in diabetic care.
Butterfly Needles: Safe Needle Retraction
When it comes to butterfly needles, springs play an essential role in automatic needle retraction systems, enhancing both safety and compliance in clinical settings. Our medical springs with contamination control are engineered in sterile environments to meet the hygiene demands of disposable needle systems.
PowerPacks: Consistent Mechanical Force
In PowerPacks, used in portable or wearable medical devices, power springs provide the controlled, consistent mechanical force that drives device functions such as fluid delivery, actuation, or timed movements. Their compact, energy-dense form makes them ideal for applications where space is limited but performance and reliability are vital.
Custom Spring Design for Medical Devices: Why Choose Lesjöfors
At Lesjöfors, we’re your global partner in custom medical spring development, supporting OEMs from concept to production with a worldwide network of specialized facilities. Our ISO 13485-certified processes include cleanroom manufacturing, strict traceability, and advanced testing to ensure the highest standards of quality and cleanliness.
We offer scalable, innovative solutions across manufacturing, packaging, and automation, tailored to each device and application. Backed by cutting-edge production and laboratory technology, we also prioritize sustainability by minimizing waste, recycling materials, and improving energy efficiency. Precision, performance, and responsibility are built into every spring we produce here at Lesjöfors.
Join Us at Medical Technology and Healthcare Sector Events
We’re attending a number of healthcare, pharmacy and medical exhibitions, showcasing our latest advancements in medical-grade springs and custom spring solutions. If you’re visiting any of the following events, visit our stand to learn how Lesjofors can support your next medical device innovation, from concept through to compliance.
Contact Lesjöfors for Custom Medical Spring Solutions
Lesjöfors brings together material science, precision engineering, and decades of experience to deliver springs that perform when it matters most. If you’re looking for cleanroom-manufactured springs, sterile medical springs, or guidance on spring selection, get in touch with our team of engineers today.
Medical Device Spring FAQs
Springs are used in a wide range of medical devices, including inhalers, autoinjectors, glucose monitors, butterfly needles, ‘PowerPacks’, and others.
Medical device classifications reflect risk level. Class 1 devices pose the lowest risk, Class 2 moderate risk, and Class 3 the highest, often involving life-sustaining or implantable technologies.
Lesjöfors supplies compression springs, power springs, constant force springs, stamping, bendings, deep drawn parts, torsion springs, and custom wire forms for a variety of medical applications.
We use cleanroom environments, contamination control protocols, and certified processes to meet strict medical cleanliness standards. We also have state-of-the-art washing technology in our production sites.
Yes, we can engineer custom springs tailored to exact functional, dimensional, and material requirements.
Medical-grade materials such as stainless steel, Elgiloy, MP35N, Phynox, titanium alloys, and platinum-iridium. At Lesjöfors, we specialise in using stainless steel for our medical springs and pressings.