You’ll find wire forms in everything from household items to car parts. Forming these small yet versatile metal components involves various techniques, shapes and materials to meet the needs of the end application. These unique wire parts play an important role in almost all industries, from agriculture to aerospace.
Here at Lesjöfors, we have over 170 years of experience working with wire products, and we manufacture millions each year for some of the world’s biggest brands. In this blog, we’ll give you a complete guide to metal wire forming, from simple definitions to manufacturing techniques and ideal materials.
What is Wire Forming?
Wire forming involves bending, coiling and free-forming metal wire into specific shapes and sizes for a range of applications. From springs and clips to custom machine parts, this versatile manufacturing process creates precision parts for a variety of industries, including automotive and construction. Commonly used materials include steel, aluminum and brass because they’re flexible and strong.
The Wire Forming Process
Wire forming starts with choosing the right material, followed by cutting, bending and forming the wire into the desired shape.
Raw Material Preparation
Before production begins, manufacturers need to prepare raw materials properly for consistency and quality in the final product. This includes choosing the right metal type, cleaning it to remove impurities, and sometimes heat treating it to improve flexibility. Proper material preparation ensures smooth processing, prevents defects and enhances the final component’s strength and performance.
Essential Wire Forming Techniques
Wire manufacturing techniques vary depending on the final application. A range of manual and automated processes create everything from simple hooks to complex industrial components. Common methods include bending, coiling, stamping, and computer-led processes, such as Computer Numerical Control (CNC) wire forming, giving even more precision.
Equipment and Tools Used in Wire Forming
Producing these intricate wire components requires specialist equipment to create the desired shape accurately. CNC wire benders, wire forming machines, coiling machines, and stamping presses automate the process for accuracy and efficiency, while tools like jigs, dies and welding equipment help achieve complex shapes. Hand tools, such as pliers and cutters, assist with manual adjustments, and advanced robotics and automation enhance precision and speed, ensuring better results.
Quality Control Measures
Strict quality control ensures products meet industry standards. During production, inspections check for accuracy, strength and consistency, using tools like calipers and tensile strength testers. Automated systems look for defects, while stress testing confirms strength. At Lesjӧfors, we take quality management and environmental responsibility seriously, and we’re committed to the internationally recognized standards ISO 14001, ISO 45001 and ISO 9001.
Types of Wire Forms
Wire forms come in various shapes and sizes, serving different industries and applications. They can be standard or custom-designed, depending on your specific needs.
Standard Wire Forms
Standard wire products can include springs, hooks, clips and rings. Manufacturers produce these pre-designed shapes in bulk to meet general requirements. Their reliability, durability and relatively low cost make them ideal for cars, construction and household products. At Lesjöfors, we have the widest range of standard wire products in the industry.
Custom Wire Forms
Suppliers can also design and manufacture custom shapes to meet individual specifications. Using advanced CNC machinery and precision bending techniques, manufacturers like Lesjӧfors create complex shapes to suit the unique needs of industries like aerospace, healthcare and electronics. Custom products can mean better performance, reliability and functionality in demanding environments. From product design and prototyping to testing and manufacturing, at Lesjöfors, our expert engineers work with individual clients to create custom wire forms for almost any application.
Common Applications
Wire forms are widely used as springs, pins, fasteners and clamps in automotive, construction, medical and electronics industries. Their versatile nature and strength make them ideal for structural support, electrical connections, and mechanical components.
Material Options
When producing wire products, the material choice depends on the application, considering factors like strength, flexibility and corrosion resistance. At Lesjӧfors, for example, we manufacture wire products from various materials, including stainless steel, nickel alloy and chrome silicon steel, as well as copper, titanium alloy, and high-performance super alloys like Inconel, Hastelloy and Nimonic.
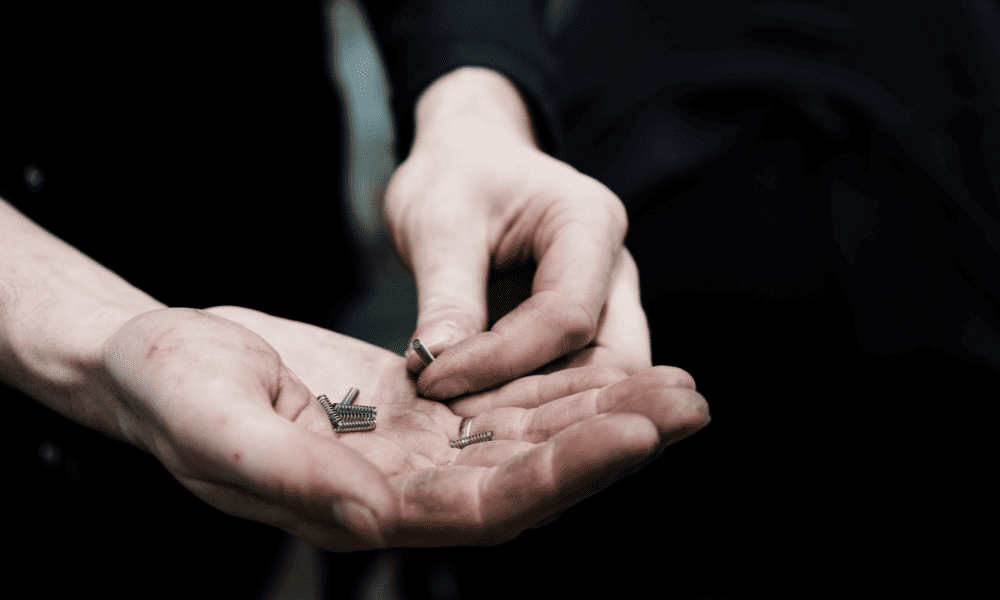
Wire Forming in Design
Design Considerations
When designing wire forms, engineers must consider material, shape, load requirements and environmental conditions. Factors like bend radius, stress distribution and manufacturing tolerances impact the performance and longevity of the final product and added coatings and finishes can boost corrosion resistance. A well-designed wire product will be more reliable, efficient and durable in its final application.
At Lesjӧfors, we deliver custom-designed, precision-engineered solutions. Our engineers work with our clients to customize length, force, movement, damping, connectors, color and finish, ensuring the best product performance.
Prototyping with Wire Forms
Prototyping allows manufacturers to test products before full-scale production, reducing errors, saving costs, and enhancing product reliability. Using computerized simulations, 3D modeling, and robust endurance testing, engineers refine shapes, strength and flexibility, guaranteeing quality and performance in the final product.
Integration with Other Manufacturing Processes
During the design process, engineers will consider how a wire form integrates into other manufacturing processes. This makes sure the component fits seamlessly and efficiently into your production while avoiding waste and maintaining high-quality standards.
Sustainability Aspects
From environmentally responsible materials to efficient production, wire form manufacturers need to do their part to curb climate change. At Lesjӧfors, sustainability is at the core of our global operations. We’ve embedded Environmental, Social and Corporate Governance (ESG) criteria into our group’s strategy and we’ve committed to a roadmap that outlines emission reduction targets in line with the Paris Agreement.
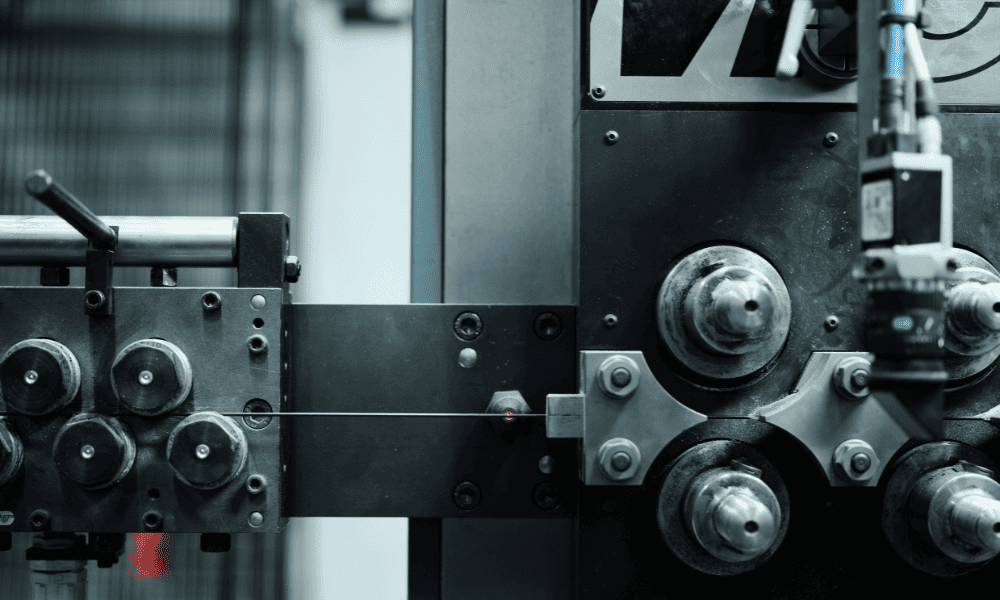
Industry Applications
Automotive
Wire forms play an important role in the automotive industry. You’ll find them in suspension systems, seat frames and engine components. Their strength and flexibility mean reliable performance in high-stress environments.
Construction
In construction, wire forms are used for reinforcement, fasteners and structural supports. Their ability to withstand heavy loads and environmental conditions makes them essential for safety and stability in building projects.
Electronics
Wire forms feature widely in electronics as connections in circuit boards, antennas and batteries. Their ability to conduct electricity, bend easily, and fit into small spaces means they’re in many electronics, from copiers and printers to vacuum cleaners and refrigerators.
Medical Devices
The medical industry relies on wire forms for surgical instruments, stents, orthopedic implants and prostheses. Made from non-toxic materials, they provide precision, durability and safety in critical healthcare environments.
Consumer Products
Everyday products like kitchen items, furniture and sporting equipment include wire forms. Their versatile nature allows for ergonomic designs, as well as improved lifespan and functionality.
Bespoke Springs & Wire Forming Solutions
Specialist manufacturers can form wire into just about any shape and you’ll find them in a wide range of industries and applications, from medical devices to everyday machines.
At Lesjӧfors, we’re a leading manufacturer of wire products. We produce quality, high-performance wire components to individual specifications, and our expert team of engineers is here to work with you to create custom solutions to meet your exact needs. Our products are precision-engineered and rigorously tested to ensure strength and durability. Contact our team today to find out more.
FAQs
Wire bending shapes wire by making simple bends, while wire forming includes a range of techniques, such as bending, coiling, twisting and cutting, to create more complex shapes.
Wire forming materials include stainless steel, aluminum, copper, brass and titanium.
The wire forming process is highly accurate, often achieving precise tolerances down to fractions of a millimeter.
The wire forming process can take anywhere from seconds to minutes, it depends on the production volume, complexity and materials.
At Lesjofors, we can create wire forms from 0.1 mm to 65 mm, with larger sizes available on request.
Wire forming is generally cost-effective, especially for high-volume production with minimal waste and automation.